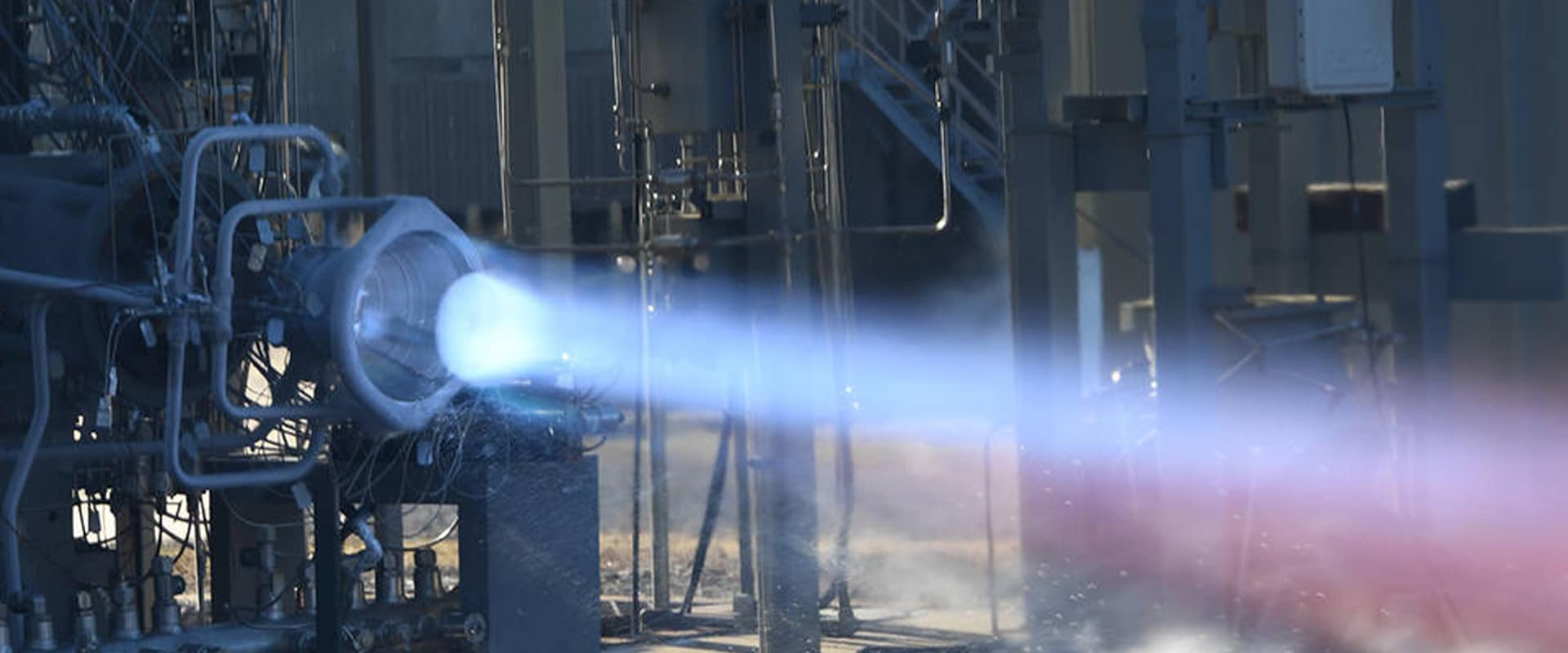
The Future of 3D Printed Rockets and Spacecraft Manufacturing
3D printing is fast becoming an exciting technology for spacecraft manufacturing and especially rockets. Both startups and established manufacturers are adopting 3D printing to create rocket components with improved design and performance at lower cost and faster turnaround times.
This technological advance is important as it allows us to manufacture the most difficult and expensive rocket engine parts at a lower price tag than in the past,” said Drew Hope, Director of the Development Program at NASA. It will also allow companies within and outside the aviation industry to do the same and apply this manufacturing technology to the medical, transportation and infrastructure industries.
Why is 3D printing used to produce rocket components?
The race to bring satellites into space is getting fiercer. Therefore, spacecraft manufacturers are faced with the challenge of accelerating the development and production of rocket while lowering costs and increasing efficiency. However, in traditional rocket manufacturing, multiple prototyping cycles and manufacturing steps make the process long and very costly. For example, it can take 10 to 14 months to build a conventional combustion chamber (a structural rocket component in which a mixture of fuel and compressed air is fired). To produce these combustion chambers, manufacturers must pour and forge individual components. The cooling ducts then have to be machined around the room – a time consuming, labor intensive and costly process. Given these challenges, major rocket manufacturers are starting to produce combustion chambers with additive manufacturing. Once designed, a 3D-printed combustion chamber can be produced within a few weeks, significantly reducing manufacturers’ production times and costs.