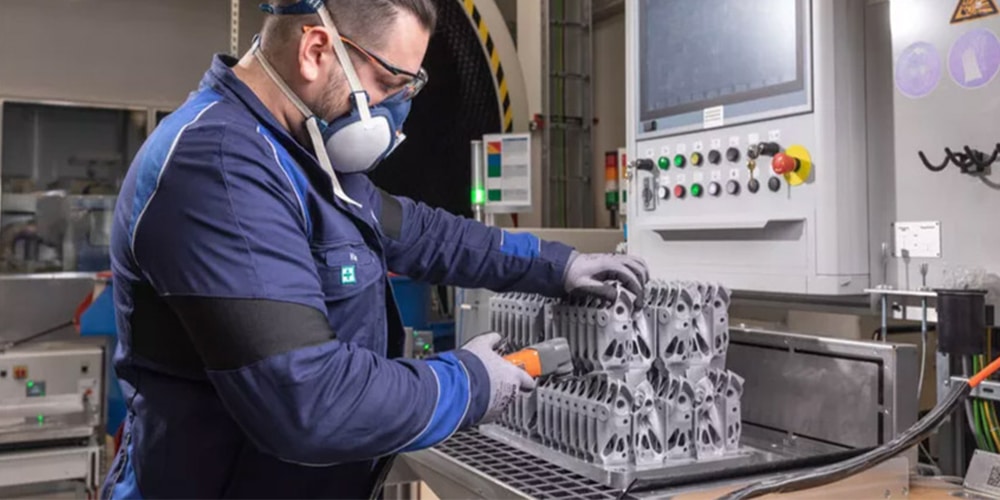
Rolls-Royce Integrates 3D Printers Into Production Process
The BMW Group is taking the next step in the systematic integration of additive manufacturing. The aim is to scale additive manufacturing down to industrial levels and to establish it systematically in various areas, including development and manufacturing, for positive economic impact. The BMW Group takes full advantage of 3D printing technology, which offers fast availability of components, flexible component design and the ability to produce parts without tools.
Daniel Schäfer, Senior Vice President of Production Integration and Pilot Plant at the BMW Group: “Processes like additive manufacturing help us speed up development processes and bring vehicles to maturity faster. 3D printing meets demanding quality requirements while shortening the production times of components. ”
Fast Production
Since mid-this year, the BMW Group has been producing metal and polymer parts for Rolls-Royce Motor Cars using additive manufacturing. The production chain is carried out in various global production networks, in different facilities at various points.
Relevant 3D components for vehicle body and passenger compartment. It is highly functional and robust. 3D printing technologies used in the entire production process were developed by the BMW Group for application in automotive production.
Landshut metal parts at the BMW Group Plant are currently produced using the SLS method. In production, metal 3D printed components are fitted into car bodies in an almost fully automated process. Polymer components from the Additive Manufacturing Campus and metal substrate for the trim panel are attached to the cars.
Component Development Through Generative Design
The extent to which additive manufacturing can be used in part production was determined in the early stages of vehicle development. Manufacturing and materials experts, as well as engineers, studied hundreds of components, focusing on the economic benefits of new technology and the weight and geometry advantages over traditionally manufactured parts. Components were selected for 3D printing based on a set of criteria and requirements defined with the help of data scientists and translated into “machine language”. This marks the start of a new artificial intelligence system that enables the BMW Group to identify faster and earlier which components could potentially be 3D printed.
Parts that were previously impossible to realize were planned with a generative design mind using computer algorithms for rapid component development. Experts created parts that ensure the best possible use of materials in design and production. Many potential applications are only possible thanks to generative design, and 3D printing technologies are a particularly suitable method for creating complex forms and structures that were previously impossible to produce with conventional tools.
For the BMW Group, generative design resulted in topology-optimized solutions where form and function were significantly improved. The components are about 50 percent lighter than similar conventional components and make the best possible use of available space, such as the shock absorber for the tailgate.
Additive Manufacturing Campus
Since June, the BMW Group has brought together all its technology expertise at its Additive Manufacturing Campus just outside Munich. The new campus also trains employees from around the world to use new technologies and is the center of prototype component manufacturing. Currently the center of excellence has close to 80 employees and currently operates about 50 metal and polymer processing systems. More than 50 systems are operating at other manufacturing sites around the world.
For more detailed information, read the original article.
3D printing technologies continue to touch every part of the industrial area day by day. In the industrial field, especially mold production takes a long time and is quite costly. Consequently, it falls short of producing qualified solutions in addition to 3D printing technology. 3D printing technology gets ahead in every aspect; it reduces costs and saves time. Much more complex components are easily produced.
It is now easier to include the developing 3D printing technology in your industrial production process.
With Zaxe Z1+ 3D printer, you can make your industrial parts production much faster and monitor a qualified production process.