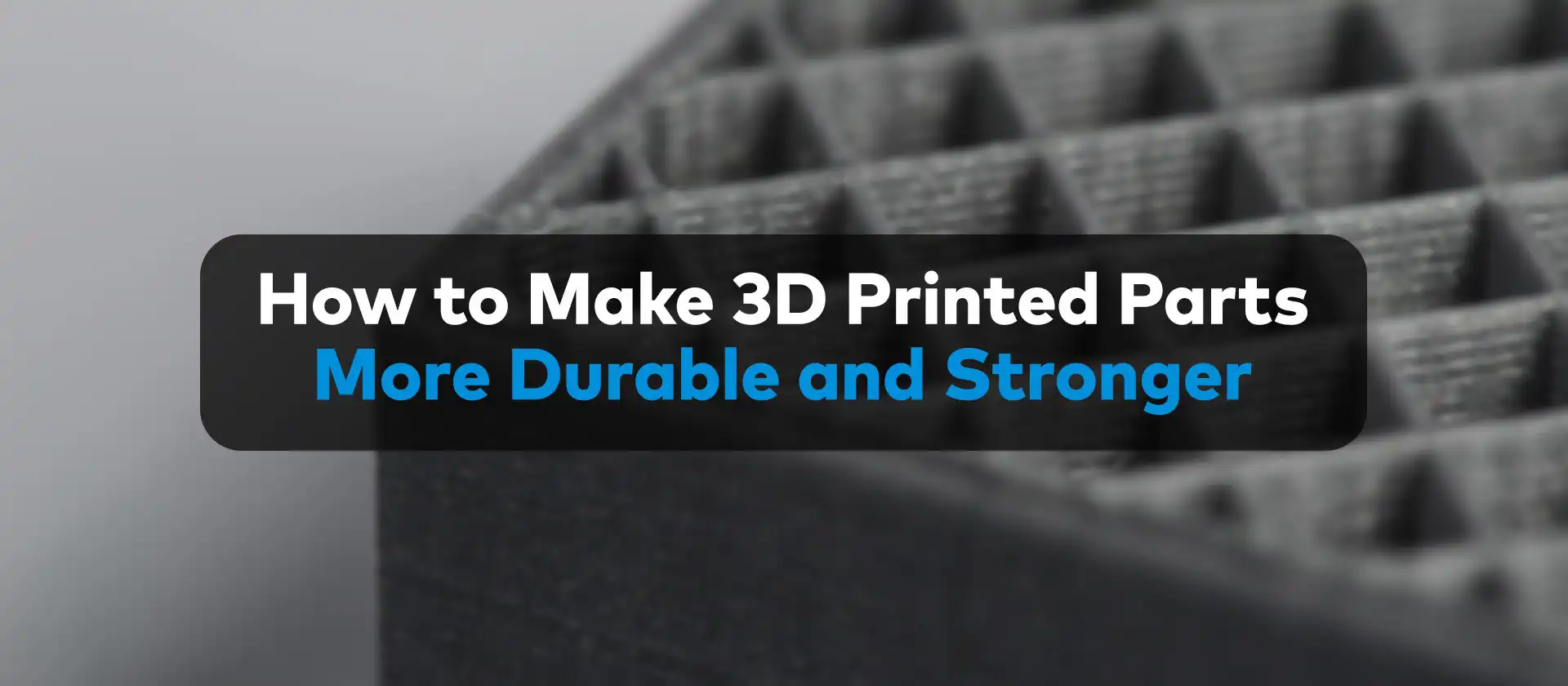
How to Make 3D Printed Parts More Durable and Stronger
The ability of additive manufacturing to produce high-quality end-use products has convinced countless businesses to start implementing 3D printers in their manufacturing lines. But people who manufacture end-use parts will discover that the quality and performance of the printed parts will differ depending on various circumstances.
Most hobbyists figured out how to make decent-looking prints with smooth finishes, but manufacturing an end-use part that will have longevity is a whole another thing. In this guide, we will give a couple of tips on how to achieve durable parts that will serve you for a long time.
Things to Consider
While we plan to make this article a general guide on the subject and keep the information we give on a practical level, there are still some things to consider before setting out to make your 3D printed parts stronger. Strong is a relative term and different parts will require different properties to perform their best in their working environment. Before printing the parts, think about the different factors that will come into play while the 3D printed parts are working and decide on some of the properties and settings depending on these factors.
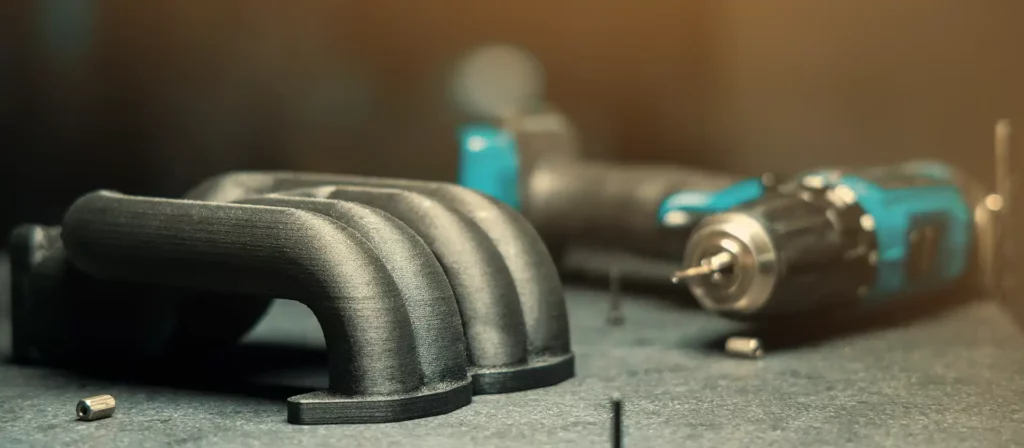
Environment
The environment that the parts will perform in will play a huge role in the longevity of the part. Heat, humidity, and different substances that the part will come into contact with can have a detrimental effect on it. For example, if the part is going to see a lot of sunlight during its service life, you should be considering printing it with a filament that has good UV resistance. Or if the print is going to be a part of a big machine that tends to get very hot, you need to print it with a material that keeps its physical properties in higher temperatures.
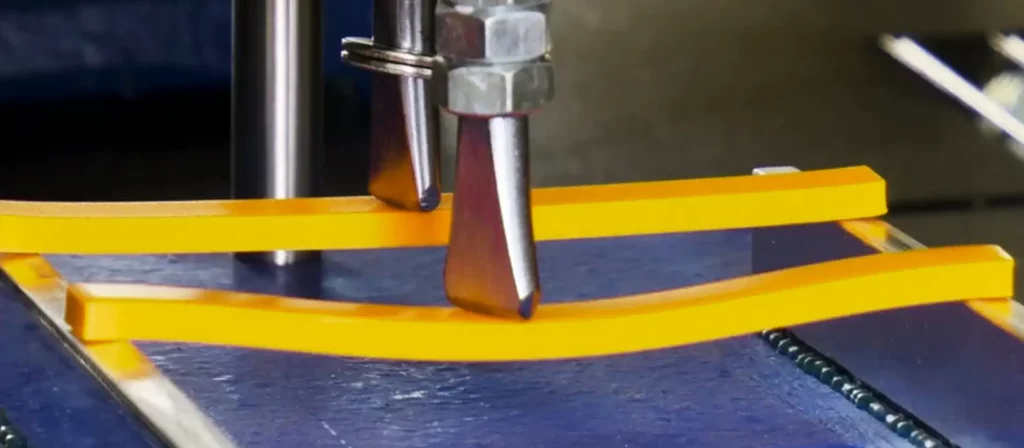
What Does Durability or Strength Even Mean?
Another thing to consider would be the meaning of durability. Obviously, there are different types of force that can be applied to a print that would have different effects on the part. For example, if you are printing a car hood, the purpose of the part should be to absorb shock as much as possible. On the other hand, if you are printing a gear for a big mechanical machine that will work for 18 hours a day, the purpose of the print should be longevity. To keep it simple, not all forces are created equal and you should take that into consideration when printing end-use parts.
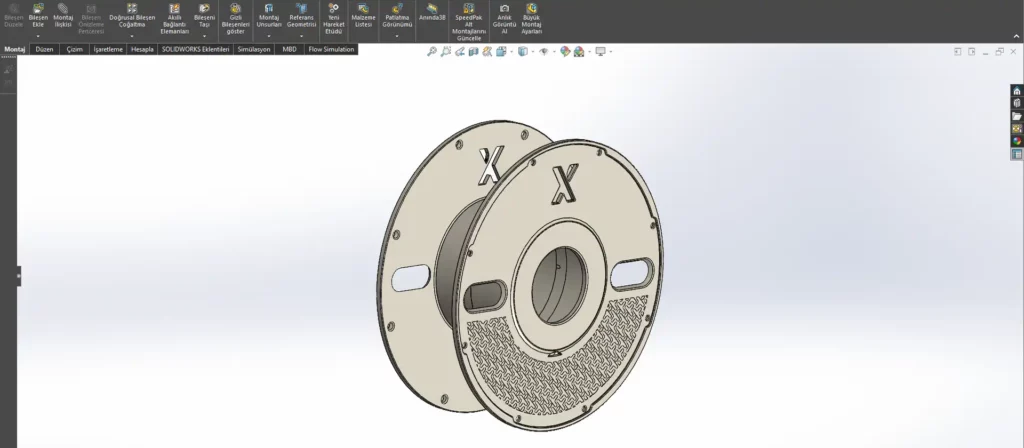
Design of the Part
The design of the product you are going to print will also affect the performance of the said product. Some design faults can also decrease the service life and quality of the part you printed to a considerable degree. These shortcomings can be so bad that the filament you printed the part with might not even matter. Bad tolerances, low structural integrity, and thin nodes that might break easily, all of these can all be prevented during the design stage and stop you from printing a subpar end-use part before it even happens.
How to Make 3D Prints Stronger
Just like a lot of other things in 3D printing, there is more than one method of achieving this goal. The biggest factor when making a more durable print will probably be the settings you use on your slicer to print the model. Some of the things you can do to achieve more durable print are;
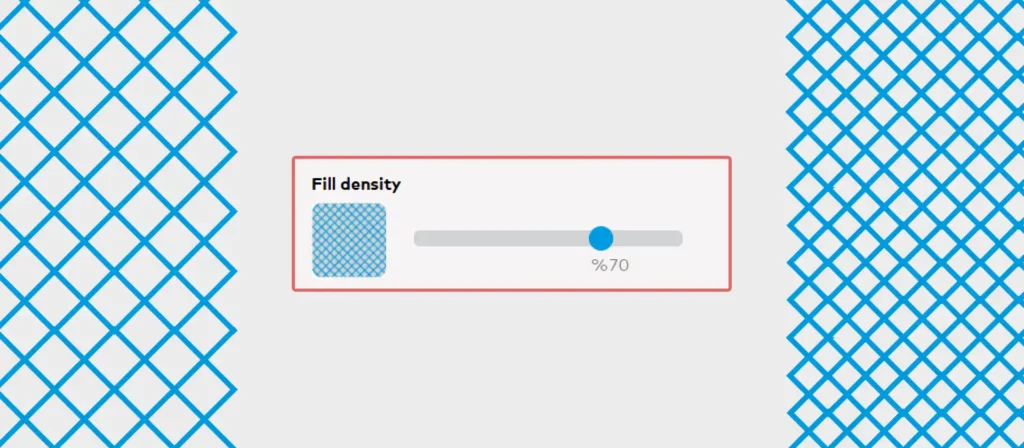
Keep the Infill Density High
One of the first things that you should pay attention to when you are trying to print stronger parts would be the infill setting you have on your slicer. This is an obvious solution for the veterans of additive manufacturing, but for the uninitiated, the infill density refers to the density of the scaffolding that your device prints inside to save time and material. Printing a model with 100% would take forever and spend way too much material. 3D printers solve this issue by keeping the inside hollow to an acceptable degree.
By increasing the infill density, you will print a sturdier and more robust part. But keep in mind that high infill density might be a double-edged sword. If you increase it too much, the print might lose some of its flexibility, resulting in a print that is more brittle.
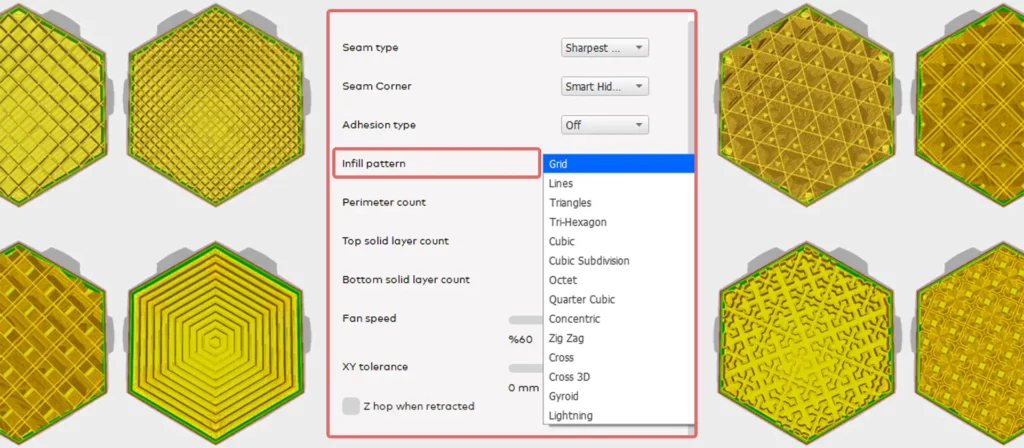
Change the Infill Pattern
The default infill pattern for most printing software is the grid and many people don’t see a problem with that. It is a well-balanced pattern that provides acceptable printing times and decent durability. But if strength is your number one priority, you can do better than grid. As we have mentioned before, it is not only a matter of sturdiness. Some parts will require a little bit more flexibility or shock absorption capabilities. The intern patterns you can use for certain properties are;
- Gyroid for increased flexibility from all angles,
- Honeycomb for shock absorption,
- Lines for flexibility from two angles,
- Triangular for overall sturdiness.
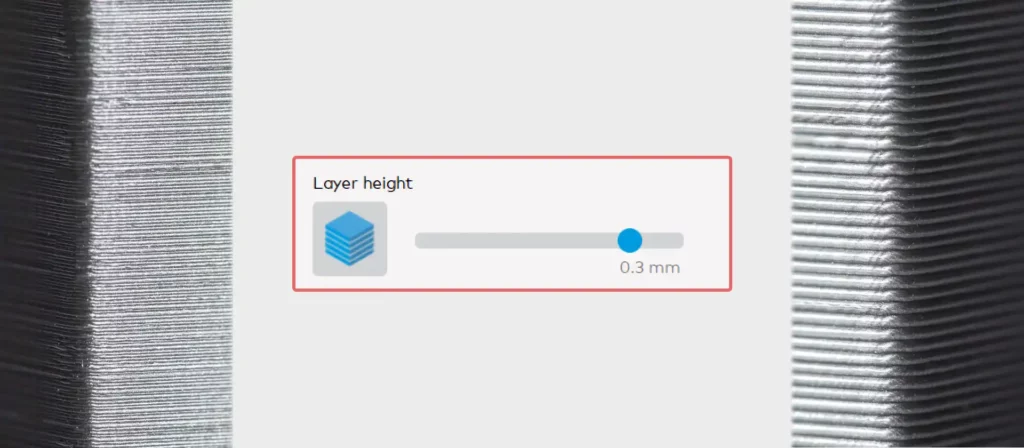
Decrease the Layer Height
As most users know by now, FDM 3D printers turn digital models into 3D objects by extruding thin layers of material on top of each other. The height of those layers depends entirely on the user and the purpose of the printed product. One of the shortcomings of FDM printing is those lines you see. Both aesthetically and structurally, those lines are a weak point for FDM prints. Not only do they look unpleasing aesthetically, but they also make the print weaker against a force that is applied at the same angle as the layer lines.
It is, of course, not that big of an issue as there are ways to eliminate this problem to a certain degree. Keeping the layer height low will work wonders for making the print more durable in all directions. This is the result of better layer adhesion that can be achieved with thinner layers and reduced gaps between the individual layers.
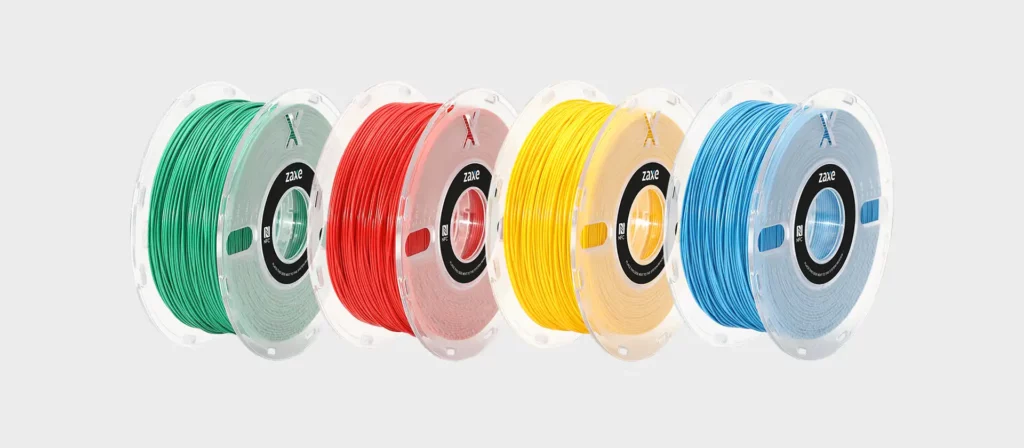
Use the Right Filament
This entry goes hand in hand with the environment entry that we talked about earlier. Different materials will shine in different environments. So, it is important to do comprehensive research on the filament type you are going to use before starting to print the parts. For example, PETG is known to perform well under mechanical stress and heat at the same time. Actually, it is the material we use to print the parts in our 3D printer at Zaxe. ASA on the other hand shines when used under sunlight due to its impressive levels of UV resistance. And finally, if the material requires a little bit of elasticity, using a flexible material will be the best course of action for you.
If you need help with deciding on which filament is the right choice: FILAMENTS 101
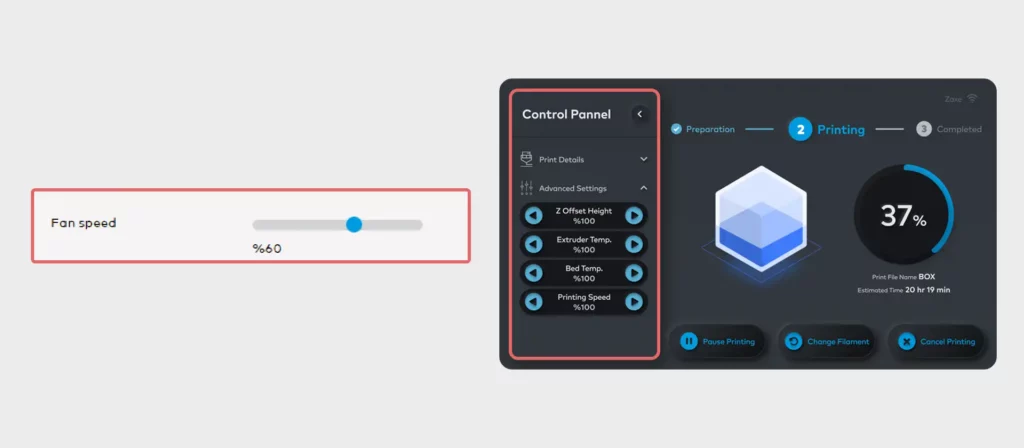
Keep the Fan Speeds Low
Proper layer adhesion is an essential part of a high-quality print. Problems like delamination or warping will all be caused by improper adhesion at some stage of the printing process. While your print might seem fine aesthetically, subpar layer adhesion might decrease the performance of an end-use product significantly. To prevent this from happening, we suggest keeping the fan speeds to a bare minimum when printing with materials that react well to heat. Higher temperatures will prevent the print from cooling off too quickly and decrease the chances of any adhesion problems like delamination and cracks between the layers.
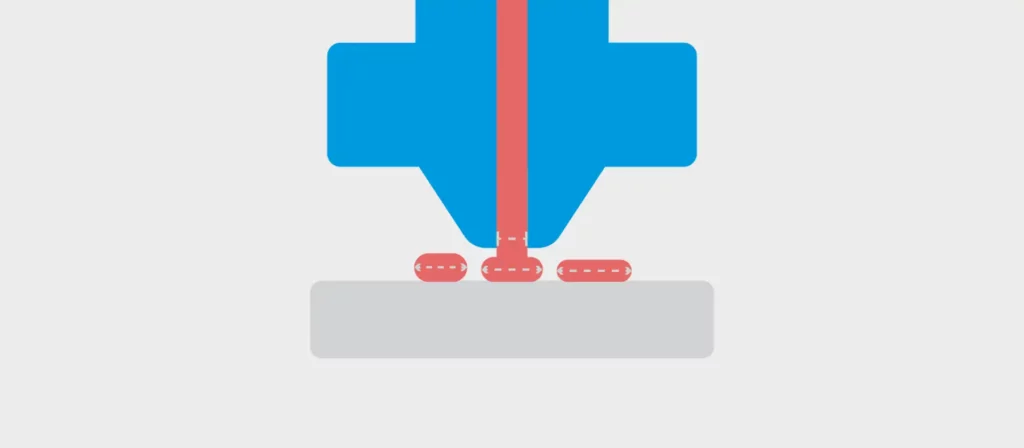
Up the Extrusion Width
If nothing else works, you can always increase the extrusion width. A thin surface wall can also decrease the durability of your prints. The accumulative wear and tear on the parts can eventually make an already fragile part brake due to a compromised outer layer. Increasing the extrusion width can increase the performance of the product by making the outer parts sturdier. Making the inner layers thicker can also result in a more robust product that will have a longer service life.
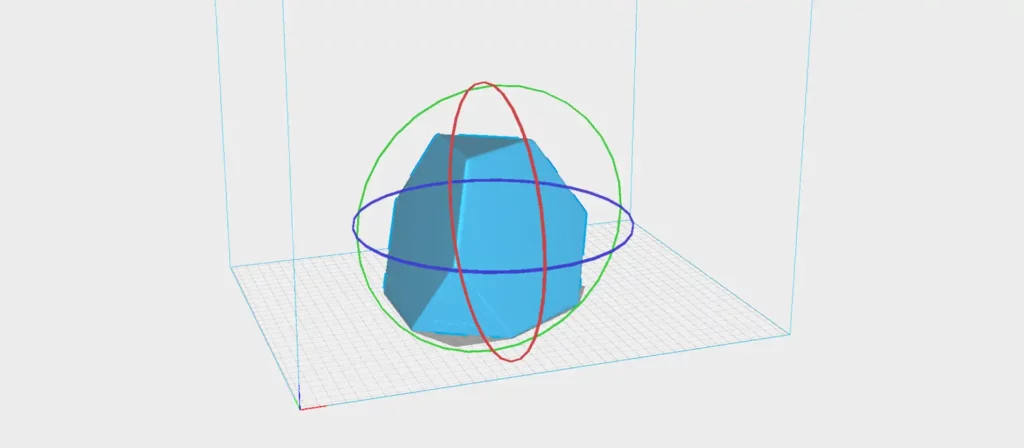
Change the Model’s Orientation
As we said, the layers lines will likely be the weakest point of your printed parts. The direction of the applied force and its relation to the layer lines will dictate a lot of things about the performance and longevity of your prints. That’s why we suggest changing the orientation of the print according to the expected angle of the different types of force applied. Or try to keep the lines as long as possible to avoid any weak points becoming parallel with the layer lines.
To Summarize
There are tons of things you can do to improve the performance and the quality of the models you print. Trial and error is the best teacher in this case but the information we have provided here will set you on your way to achieving more durable prints. Choose the right filament, adjust the settings on your slicer optimally, consider the duty of the part and keep proper orientation in mind and you will eventually get the performance you seek from the parts you print.